more 31 - 15 fix'n
#1
Senior Member
Thread Starter
Join Date: May 2012
Posts: 911

I see people buying these and other commercial machines, Then after having them, don't like the speed they run at.. To often thats because of there clutch, unlike the clutch in a car these have to slip to control the speed. Most these machines have been sitting unused for many years, so there clutch will grab and run at the speed the motor goes.
Mr Rays did a write up on installing a speed reducer, that he already had. otherwise to buy those it's $150 , but for that price to your door you could have a new servo motor, those come with new light, switch cords bolts everything needed .
being poor , I tired changing pulleys. I'm unlucky and my motor a singer motor ( on this one) you can not change out the lower pulley
you have to go to a smaller pulley at the motor to slow the speed, doing this will work, but it loose it's torque / punching power. I did this on one with an arrow motor that has changable pulleys out come was.. couldn't sew a wet paper bag on a 100 degree day.
SO, you can remove the hand wheel and replace that with a common larger pulley, which look like dog doo. out to the shop I went and made this, which cut the top speed in half and must have double the torgue
even on leatherwork (wed site) I have never seen anyone talk about making this type of upper pulley. It just slips over the factory hand wheel , I went cheap by using bolts and tabs to secure it to the handwheel
this started life as a 1/2" thick 5"x5" square piece turned down to 4 1/2" factory pulley is 2 1/2"
I'm sure counting the alu piece and machine shop would want over $75 to make one but if you have lathe, This Idea just might give you something to do someday.
Mr Rays did a write up on installing a speed reducer, that he already had. otherwise to buy those it's $150 , but for that price to your door you could have a new servo motor, those come with new light, switch cords bolts everything needed .
being poor , I tired changing pulleys. I'm unlucky and my motor a singer motor ( on this one) you can not change out the lower pulley
you have to go to a smaller pulley at the motor to slow the speed, doing this will work, but it loose it's torque / punching power. I did this on one with an arrow motor that has changable pulleys out come was.. couldn't sew a wet paper bag on a 100 degree day.
SO, you can remove the hand wheel and replace that with a common larger pulley, which look like dog doo. out to the shop I went and made this, which cut the top speed in half and must have double the torgue
even on leatherwork (wed site) I have never seen anyone talk about making this type of upper pulley. It just slips over the factory hand wheel , I went cheap by using bolts and tabs to secure it to the handwheel
this started life as a 1/2" thick 5"x5" square piece turned down to 4 1/2" factory pulley is 2 1/2"
I'm sure counting the alu piece and machine shop would want over $75 to make one but if you have lathe, This Idea just might give you something to do someday.
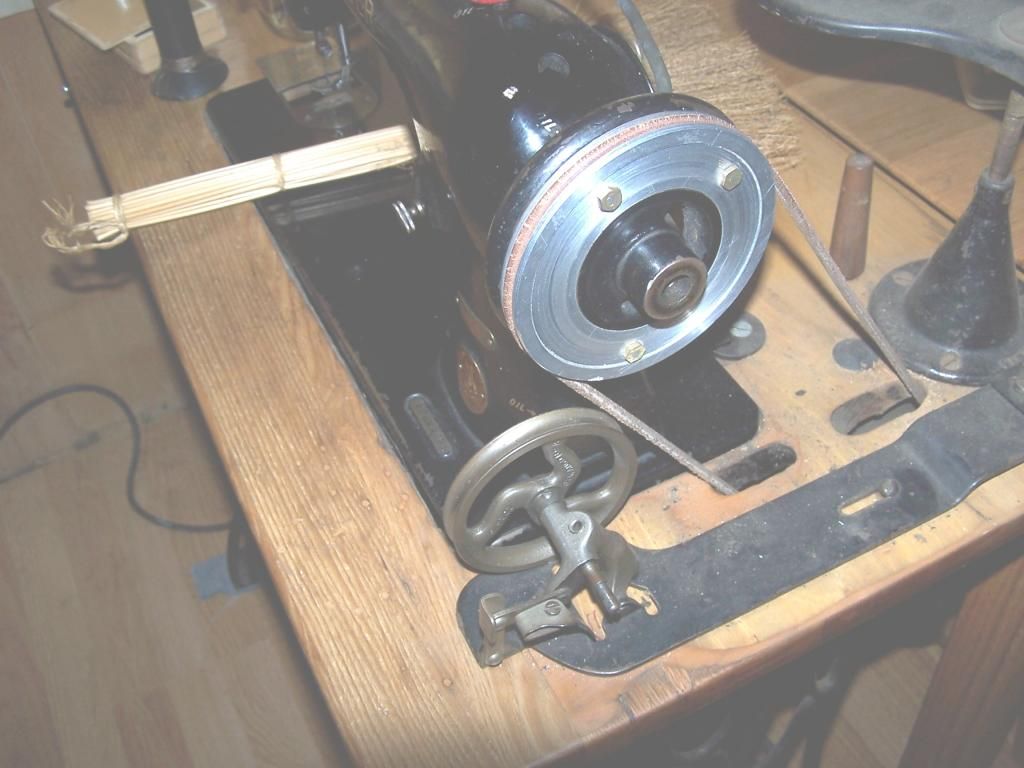
Last edited by xxxxxxxxxx; 09-09-2014 at 04:36 PM.
#2

Thanks for showing your method of slowing your 31-15 down. I like the looks of it, but I don’t have a lathe to make one.
The three ways that I have seen work to slow down a Singer 31-15 are:
Slow: On one of my 31-15s I put together a home-made speed reducer out of pulleys, bolt, and bracket. It made about a 4:2 ratio, which wasn’t quite slow enough. It reduced the speed by about half (1725RPM motor), but the machine was still fairly speedy.
Slower: I had another 31-15 that came to me with an Atlas Clutch on it that was an early style of clutch motor. The motor and clutch are two separate units. The clutch slippage can be tweaked to get a slower speed, and I’ve heard that operators even greased the cork clutch surface to increase slippage. Whoever had this one before me had tuned it very well, and I was surprised at the slow control that I could achieve.
Slowest: My go-to Singer 31-15 is in an industrial treadle. I have no problem sewing as slow as I want. I also have a 31-15 that I’m experimenting with a spinner steering wheel knob on it to use for hand operation. It should be slower than the treadle.
CD in Oklahoma
The three ways that I have seen work to slow down a Singer 31-15 are:
Slow: On one of my 31-15s I put together a home-made speed reducer out of pulleys, bolt, and bracket. It made about a 4:2 ratio, which wasn’t quite slow enough. It reduced the speed by about half (1725RPM motor), but the machine was still fairly speedy.
Slower: I had another 31-15 that came to me with an Atlas Clutch on it that was an early style of clutch motor. The motor and clutch are two separate units. The clutch slippage can be tweaked to get a slower speed, and I’ve heard that operators even greased the cork clutch surface to increase slippage. Whoever had this one before me had tuned it very well, and I was surprised at the slow control that I could achieve.
Slowest: My go-to Singer 31-15 is in an industrial treadle. I have no problem sewing as slow as I want. I also have a 31-15 that I’m experimenting with a spinner steering wheel knob on it to use for hand operation. It should be slower than the treadle.
CD in Oklahoma
#4
Senior Member
Thread Starter
Join Date: May 2012
Posts: 911

Cd ,
we know these have a cast in motor boss on them. so singer must have made a motor for that. I have seen ones on C/L for sale that did have some kind of motor mounted there, but look much bigger than the standrad SM motor. I did take a 1.3 amp motor and set that up. but all I had was a piece of old leather belt. when I would hit a heavy seam that belt would slip. Thinking a v belt might have worked. This was using a no so great 31 - 20 wore out race, so it's a bit sticky..
I have two treadle type stands for these, each is missing the wheel. I have spare home type stands now, so I'm playing with the idea of mounting the table top higher so the larger machine will clear the legs and see what the smaller 12" flywheel will do for power LLOL.
Then I saw a machine F/S that had a regular pulley on top that must have been 8 + inches. which is to big , to much of a chance of something getting caught in it like your sleeve and ripping off your arm
anyway those pulleys here are around $25, the piece of alum I made this pulley from, if I had to buy it would have been over $20, add the bolts and gas to go get it. For me is over a 100 mile drive. all this playing adds up quick.
The sevro motors I see the cheapies for $99 shipped, the so called better 550 watts shipped at $120
afew years ago I bought a new arrow motor, works great after breaking in the clutch. This came off a Brennia ( sp ? ) 950 The lady put a servo on that, she loves it.. now
I have had all these clutch's apart (5) noted that the older ones have a lot of grease on them from there ball bearings with no seals ? and how those are service greased, I've ask service guys if the friction surface should be oiled, no one says yes or no.
on the leather working sites, they never seem to get into talking about this type of thing ..
we know these have a cast in motor boss on them. so singer must have made a motor for that. I have seen ones on C/L for sale that did have some kind of motor mounted there, but look much bigger than the standrad SM motor. I did take a 1.3 amp motor and set that up. but all I had was a piece of old leather belt. when I would hit a heavy seam that belt would slip. Thinking a v belt might have worked. This was using a no so great 31 - 20 wore out race, so it's a bit sticky..
I have two treadle type stands for these, each is missing the wheel. I have spare home type stands now, so I'm playing with the idea of mounting the table top higher so the larger machine will clear the legs and see what the smaller 12" flywheel will do for power LLOL.
Then I saw a machine F/S that had a regular pulley on top that must have been 8 + inches. which is to big , to much of a chance of something getting caught in it like your sleeve and ripping off your arm
anyway those pulleys here are around $25, the piece of alum I made this pulley from, if I had to buy it would have been over $20, add the bolts and gas to go get it. For me is over a 100 mile drive. all this playing adds up quick.
The sevro motors I see the cheapies for $99 shipped, the so called better 550 watts shipped at $120
afew years ago I bought a new arrow motor, works great after breaking in the clutch. This came off a Brennia ( sp ? ) 950 The lady put a servo on that, she loves it.. now
I have had all these clutch's apart (5) noted that the older ones have a lot of grease on them from there ball bearings with no seals ? and how those are service greased, I've ask service guys if the friction surface should be oiled, no one says yes or no.
on the leather working sites, they never seem to get into talking about this type of thing ..
#5
Senior Member
Thread Starter
Join Date: May 2012
Posts: 911

and I've been trieng to chase down the handwheel off a old commercial type gate valve. like a huge water faucet or a 29K size handwheel and adapt that to these , cause I find in doing leather with my 16 - 188's I do use just the hand wheel on the small stuff. which would be nice if it were larger
just more thinking , to much thinking .
just more thinking , to much thinking .
#6

Can you comment on the piercing power you get from the industrial treadle vs your other 31-15 models? Is it the same/similar/weaker than the others?
#7
Super Member
Join Date: Oct 2013
Location: Centralia, WA, USA
Posts: 4,890

and I've been trieng to chase down the handwheel off a old commercial type gate valve. like a huge water faucet or a 29K size handwheel and adapt that to these , cause I find in doing leather with my 16 - 188's I do use just the hand wheel on the small stuff. which would be nice if it were larger
just more thinking , to much thinking .
just more thinking , to much thinking .
Rodney
#8

I have a Singer 95-40 that came to me with a motor mounted onto the lug under the handwheel, but the motor had taken a “hit” and was broken. It was obviously an add-on by a user. Something that someone cobbled together, including the bracket. I don’t recall ever seeing an original Singer lug-mounted motor on these type machines, but there has to be a reason for the lug.
I know a lady in Arkansas that mounted a regular 12.5” flywheel in her Singer industrial treadle stand, and used two pitman rods clamped together for added length, in which she operated a 1969 Bernina machine. She said that other than being a tad noisy, it worked just fine, but she wasn’t sure the arrangement would power an industrial machine. She recently obtained a 16” flywheel (normal size) to exchange with the smaller wheel, but hasn’t made the conversion yet. I’m curious what the speed and torque differences will be, because I have an industrial stand that I want to try the small flywheel in for an industrial machine, hoping to have a slower speed but adequate power.
I saw a YouTube video of a fellow that removed the 16” flywheel from his Singer industrial stand, and installed the flywheel off of his Singer 29 Patcher in its place trying to reduce the speed of a Singer 31K, but I’m not sure how well it worked. The flywheel of a Singer 29 has two pulleys, an 8.5” and a 10”. He was using the 8.5” pulley in his video. I had some doubts about some of the rest of his video, so I took the whole video with a grain of salt.
As far as piercing power, I can’t give much of an opinion on that, since I’ve not used more than one machine for the same project. Plus, I’m mostly sewing light-weight vinyl and canvas, so punching power is not an issue. Obviously, when sewing seams or hems made up of several layers, the needle does need more oomph to push it through, but I don’t know how one power method would compare to another without sewing the exact same thing on multiple machines.
CD in Oklahoma
I know a lady in Arkansas that mounted a regular 12.5” flywheel in her Singer industrial treadle stand, and used two pitman rods clamped together for added length, in which she operated a 1969 Bernina machine. She said that other than being a tad noisy, it worked just fine, but she wasn’t sure the arrangement would power an industrial machine. She recently obtained a 16” flywheel (normal size) to exchange with the smaller wheel, but hasn’t made the conversion yet. I’m curious what the speed and torque differences will be, because I have an industrial stand that I want to try the small flywheel in for an industrial machine, hoping to have a slower speed but adequate power.
I saw a YouTube video of a fellow that removed the 16” flywheel from his Singer industrial stand, and installed the flywheel off of his Singer 29 Patcher in its place trying to reduce the speed of a Singer 31K, but I’m not sure how well it worked. The flywheel of a Singer 29 has two pulleys, an 8.5” and a 10”. He was using the 8.5” pulley in his video. I had some doubts about some of the rest of his video, so I took the whole video with a grain of salt.
As far as piercing power, I can’t give much of an opinion on that, since I’ve not used more than one machine for the same project. Plus, I’m mostly sewing light-weight vinyl and canvas, so punching power is not an issue. Obviously, when sewing seams or hems made up of several layers, the needle does need more oomph to push it through, but I don’t know how one power method would compare to another without sewing the exact same thing on multiple machines.
CD in Oklahoma
#9
Senior Member
Thread Starter
Join Date: May 2012
Posts: 911

Cd what is that motor ? it looks like a straight up 110V motor ?
The one in a picture that I saw, gave me the impression ( by size and color) that it may have been the type motor used on HI end long arm quilting machines, Those are about as big around as a quart canning bottle, the one's I know of are off white in color. guessing there AC/DC so they would run off a standard pedal
The 12" flywheel vs a 16". I tried this. it will go in there on the big stand but the bolt / screw and lock nut. in order to get a decent adjustment at the wheel the screw head was inside the casting on the frame, I had to put the lock nut inside next to the wheel, it was still a bit sloppy, leaving only a few threads in the frame. so the cranks arm was a bit to short on the home version wheel
Then the pitman arm did line up, this was using the steel pitman type. I checked this morning and now have to wonder if using the wooden pitman type and making a new arm / rod that these smaller wheels might be a go..
The only complete industrail treadle I have is a ww d 12 the punching power is fine, on thick leather I do have the handwheel the first hole, leather as use for chaps ect no problem, by thick i mean leather use in mill aprons halters, and two thicknesses of that. again because of keeping the design and straight lines this is done by hand wheel, Those d12 have a large wheel.
my reason on using a gate valve wheel is size, but The size has to do with ease of reaching over and finding the wheel without looking.. not it's weight a gate wheel would not have a pulley, so using one of those the machine would be handwheel only
I've even toyed with making a wooden hand wheel, it could be made of oak and designed to look like a spoked wheel using a steel hub. no belt.
I have that 31-20 with a wore out race and who knows what else, it sews good at as low speed, under power it skips. if you check prices on 31-20 parts oh boy 3 times of what 31-15 parts are. I think the 20 can be converted to a 15 ??. anyway just thinking of a cheap way of putting this 31-20 back online ..
I can turn 9 1/2" stock in my lathe, it's a metal lathe, but I do turn spindles of the broken ones on cabinets in it, not so easy but doable.
The one in a picture that I saw, gave me the impression ( by size and color) that it may have been the type motor used on HI end long arm quilting machines, Those are about as big around as a quart canning bottle, the one's I know of are off white in color. guessing there AC/DC so they would run off a standard pedal
The 12" flywheel vs a 16". I tried this. it will go in there on the big stand but the bolt / screw and lock nut. in order to get a decent adjustment at the wheel the screw head was inside the casting on the frame, I had to put the lock nut inside next to the wheel, it was still a bit sloppy, leaving only a few threads in the frame. so the cranks arm was a bit to short on the home version wheel
Then the pitman arm did line up, this was using the steel pitman type. I checked this morning and now have to wonder if using the wooden pitman type and making a new arm / rod that these smaller wheels might be a go..
The only complete industrail treadle I have is a ww d 12 the punching power is fine, on thick leather I do have the handwheel the first hole, leather as use for chaps ect no problem, by thick i mean leather use in mill aprons halters, and two thicknesses of that. again because of keeping the design and straight lines this is done by hand wheel, Those d12 have a large wheel.
my reason on using a gate valve wheel is size, but The size has to do with ease of reaching over and finding the wheel without looking.. not it's weight a gate wheel would not have a pulley, so using one of those the machine would be handwheel only
I've even toyed with making a wooden hand wheel, it could be made of oak and designed to look like a spoked wheel using a steel hub. no belt.
I have that 31-20 with a wore out race and who knows what else, it sews good at as low speed, under power it skips. if you check prices on 31-20 parts oh boy 3 times of what 31-15 parts are. I think the 20 can be converted to a 15 ??. anyway just thinking of a cheap way of putting this 31-20 back online ..
I can turn 9 1/2" stock in my lathe, it's a metal lathe, but I do turn spindles of the broken ones on cabinets in it, not so easy but doable.
#10

I don’t have the motor nearby to see if it has a name on it, but when I hooked a control to it and plugged it in it went to arcin’ and sparkin’, but it did run. If I remember correctly, the brush tube on one side was broken. It’s not original to the machine, as can be seen by the hose clamp that attaches it to the bracket. It also had a really obnoxious-looking open-wire rheostat wired to it when I got it, and I promptly removed it and put that thing in the bottom of a drawer someplace where I thought that I wouldn’t ever find it again and be tempted to use it. I didn’t even take a photo of it. It’s that dangerous-looking.
Maybe the mis-fit of the household flywheel on the industrial stand that you mentioned was the cause for the noise that my friend in Arkansas experienced with her small flywheel re-fit.
CD in Oklahoma
Maybe the mis-fit of the household flywheel on the industrial stand that you mentioned was the cause for the noise that my friend in Arkansas experienced with her small flywheel re-fit.
CD in Oklahoma
Thread
Thread Starter
Forum
Replies
Last Post
Elizabeth A.
Pictures
22
08-05-2008 05:11 PM