Treadle tubing belt revisited
#1
Super Member
Thread Starter
Join Date: Feb 2012
Posts: 8,091

I read about using aquarium tubing for treadle belts here some months ago and tried it. The tubing belt was to be wrapped around the wheels taking all the slack out, but not stretching it and cut where the end was. Then shortened by an inch or so and the cut off piece used for the coupler. To do that the short piece was slit length wise, then rolled tight and pushed into the two ends of the belt.
Here is what that looks like with my 9W-7 in the treadle:
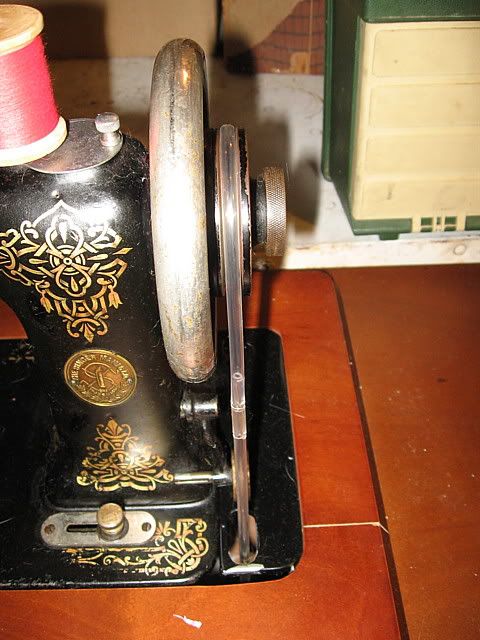
Unfortunately that didn't work as good as I thought it should. After using the belt the coupler would slip out of the ends and the belt would loose it's tension and start slipping.
So I had an idea. Make a barbed coupler out of some of the acetel rod my wife bought for her crafts. I took a length of 3/16" rod and cut off a 1" piece. Then put it in my drill motor chamfered the ends and cut groves in it for barbs.
Here is a pic of the old slit tubing couple, the acetel rod and the new coupler in the tubing belt:
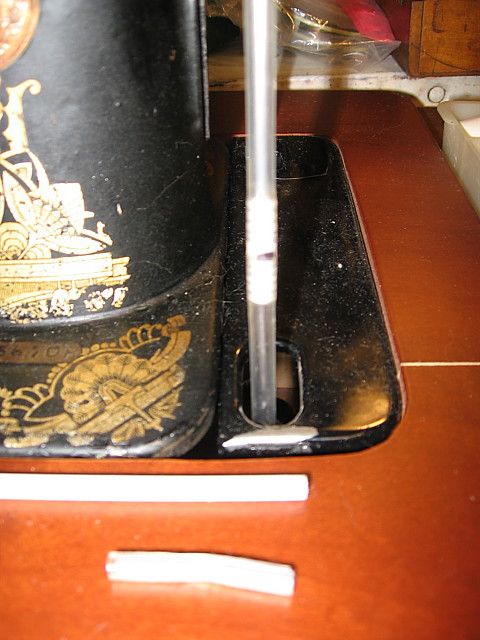
And here's a close up of the new barbed coupler in the tubing:
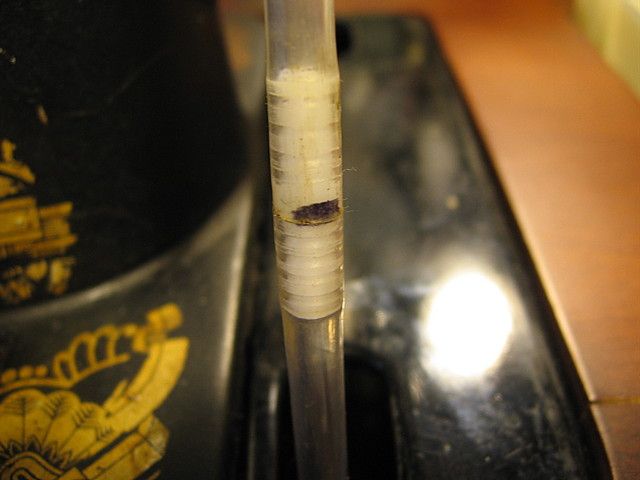
And here is the Singer 127 I'm using the tubing belt on right now:
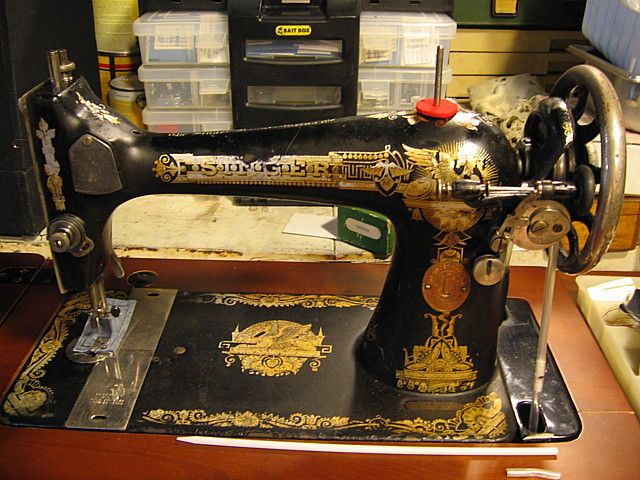
I've mentioned this one before. It's the one in my thread: I never thought it would sew again.
The new barbed coupler has held for several days and almost an entire Whacky bag of sewing. I do believe it's a much better way to keep the belt together.
Joe
Here is what that looks like with my 9W-7 in the treadle:
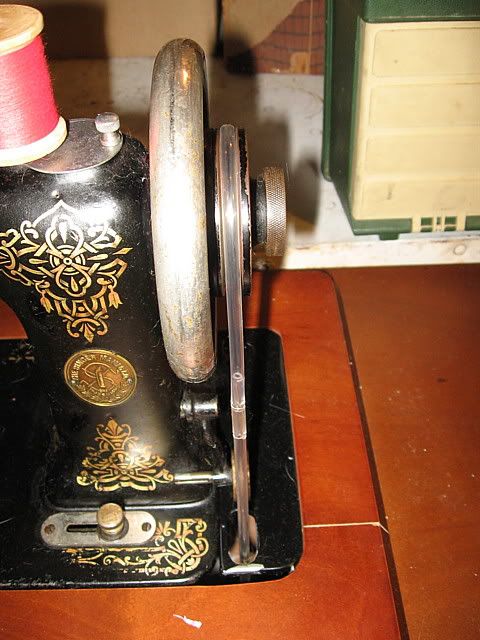
Unfortunately that didn't work as good as I thought it should. After using the belt the coupler would slip out of the ends and the belt would loose it's tension and start slipping.
So I had an idea. Make a barbed coupler out of some of the acetel rod my wife bought for her crafts. I took a length of 3/16" rod and cut off a 1" piece. Then put it in my drill motor chamfered the ends and cut groves in it for barbs.
Here is a pic of the old slit tubing couple, the acetel rod and the new coupler in the tubing belt:
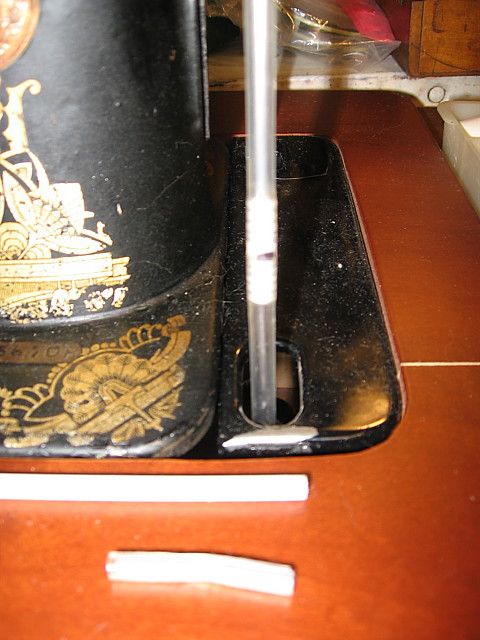
And here's a close up of the new barbed coupler in the tubing:
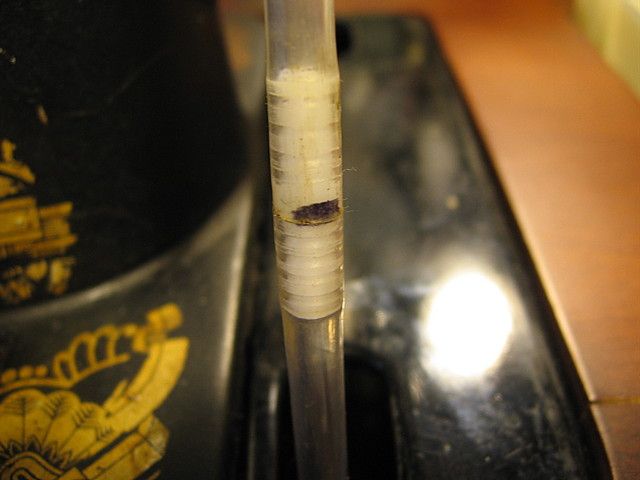
And here is the Singer 127 I'm using the tubing belt on right now:
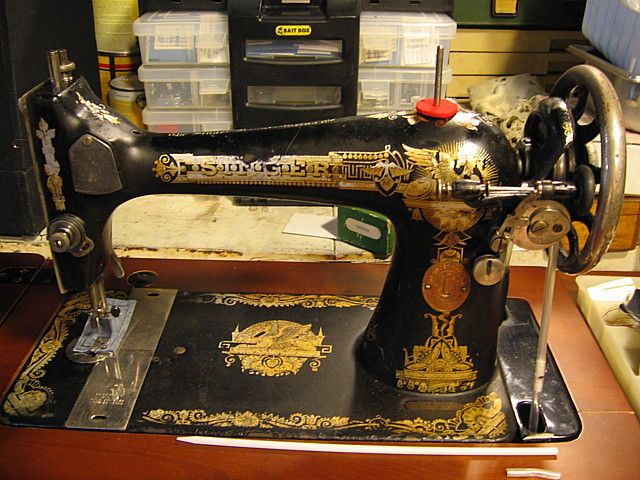
I've mentioned this one before. It's the one in my thread: I never thought it would sew again.
The new barbed coupler has held for several days and almost an entire Whacky bag of sewing. I do believe it's a much better way to keep the belt together.
Joe
#2

I had trouble when I tried to use the tubing as the coupler. I wasn't smart enough to slice it and roll it so that it would fit. I struggled and struggled trying to insert it even after cutting the coupler's ends into 'V' shapes. I ended up using the wire from a large paperclip and made a staple similar to the ones on a leather belt. I used wire cutters to make it the correct length and used needle nose pliers to shape it. Then, poked a hole in each end of the tubing so that the staple could be attached. Joe, I like your idea and I would rather I didn't have that metal staple touching my machines.
#4
Super Member
Thread Starter
Join Date: Feb 2012
Posts: 8,091

Well, I probably could have used the old belt. But I don't sew things together too good by hand. And since I have access to a bunch of the rods, it made a perfect coupler.
I suppose there's lots of ways to do it. This is one
I suppose you could also use the tubing to hold a too short leather belt together if you wanted. I might try that.
Joe
I suppose there's lots of ways to do it. This is one
I suppose you could also use the tubing to hold a too short leather belt together if you wanted. I might try that.
Joe
#6
Super Member
Thread Starter
Join Date: Feb 2012
Posts: 8,091

Patty,
I actually got the idea from the barbed couplers the automotive industry uses on vacuum tubing. I've got a link to the belt on the Lehmans site, but the pic doesn't give a good view of the coupler.
I'm gonna make a few more and put them with the remainder of the tubing for when I might need another belt.
Joe
I actually got the idea from the barbed couplers the automotive industry uses on vacuum tubing. I've got a link to the belt on the Lehmans site, but the pic doesn't give a good view of the coupler.
I'm gonna make a few more and put them with the remainder of the tubing for when I might need another belt.
Joe
#10

I read about using aquarium tubing for treadle belts here some months ago and tried it. The tubing belt was to be wrapped around the wheels taking all the slack out, but not stretching it and cut where the end was. Then shortened by an inch or so and the cut off piece used for the coupler. To do that the short piece was slit length wise, then rolled tight and pushed into the two ends of the belt.
Here is what that looks like with my 9W-7 in the treadle:
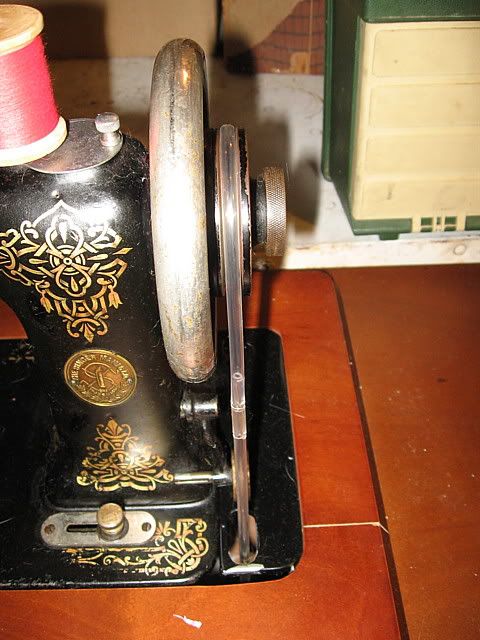
Unfortunately that didn't work as good as I thought it should. After using the belt the coupler would slip out of the ends and the belt would loose it's tension and start slipping.
So I had an idea. Make a barbed coupler out of some of the acetel rod my wife bought for her crafts. I took a length of 3/16" rod and cut off a 1" piece. Then put it in my drill motor chamfered the ends and cut groves in it for barbs.
Here is a pic of the old slit tubing couple, the acetel rod and the new coupler in the tubing belt:
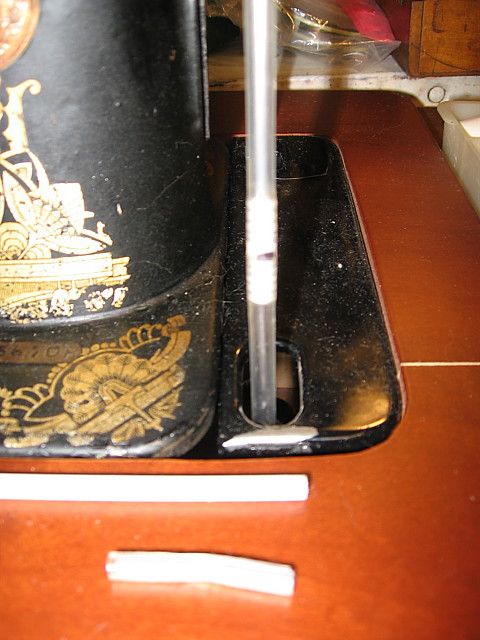
And here's a close up of the new barbed coupler in the tubing:
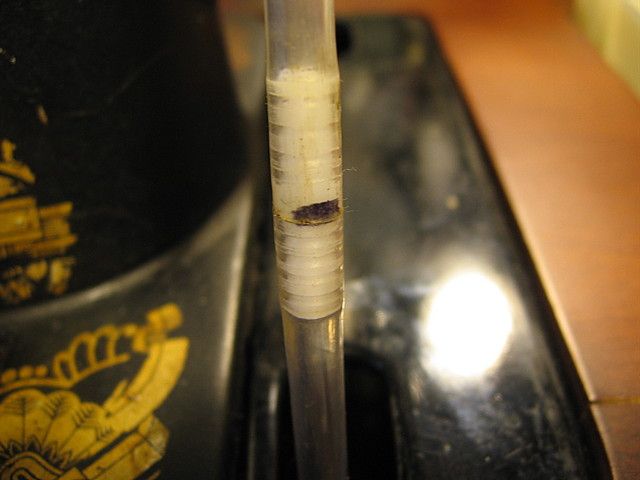
And here is the Singer 127 I'm using the tubing belt on right now:
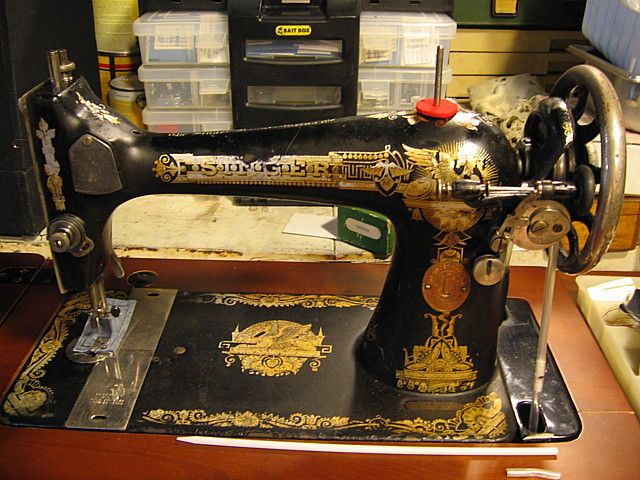
I've mentioned this one before. It's the one in my thread: I never thought it would sew again.
The new barbed coupler has held for several days and almost an entire Whacky bag of sewing. I do believe it's a much better way to keep the belt together.
Joe
Here is what that looks like with my 9W-7 in the treadle:
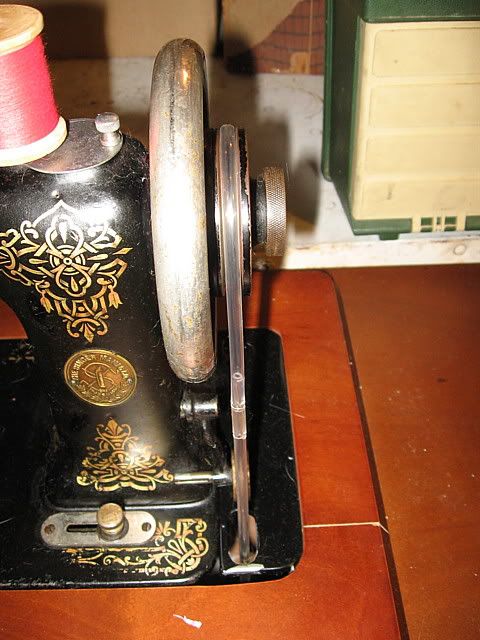
Unfortunately that didn't work as good as I thought it should. After using the belt the coupler would slip out of the ends and the belt would loose it's tension and start slipping.
So I had an idea. Make a barbed coupler out of some of the acetel rod my wife bought for her crafts. I took a length of 3/16" rod and cut off a 1" piece. Then put it in my drill motor chamfered the ends and cut groves in it for barbs.
Here is a pic of the old slit tubing couple, the acetel rod and the new coupler in the tubing belt:
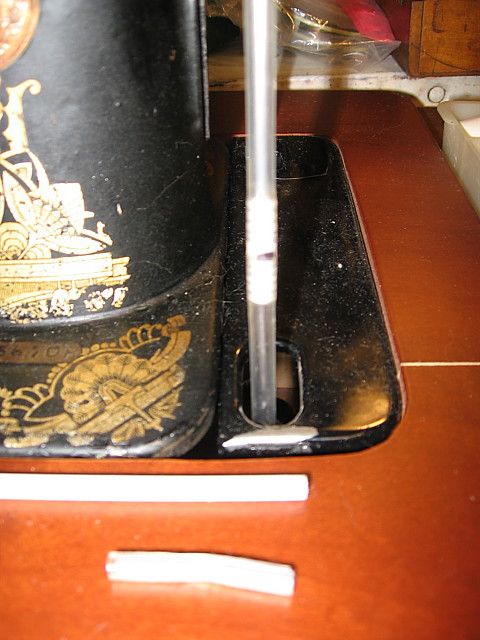
And here's a close up of the new barbed coupler in the tubing:
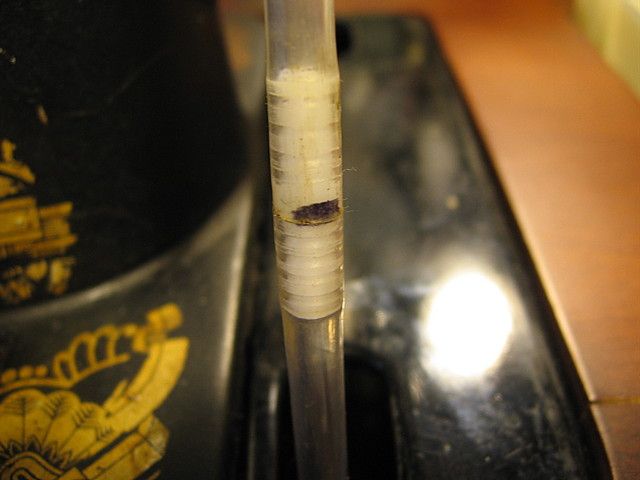
And here is the Singer 127 I'm using the tubing belt on right now:
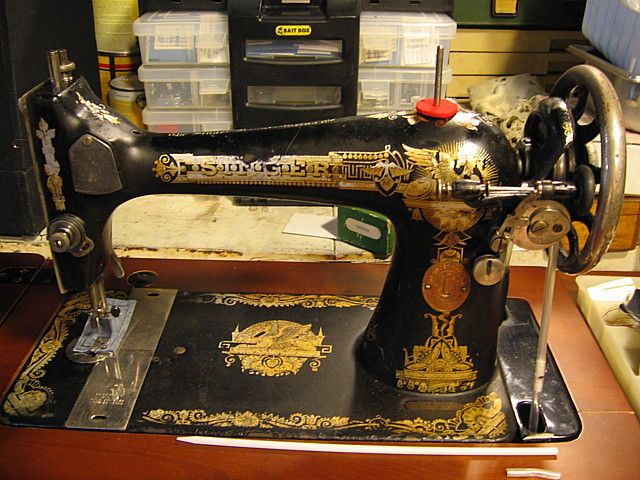
I've mentioned this one before. It's the one in my thread: I never thought it would sew again.
The new barbed coupler has held for several days and almost an entire Whacky bag of sewing. I do believe it's a much better way to keep the belt together.
Joe
JoAnn
Thread
Thread Starter
Forum
Replies
Last Post
J Miller
For Vintage & Antique Machine Enthusiasts
16
08-05-2012 04:28 AM